In industries ranging from manufacturing to energy production, rubber plugs serve as unsung heroes in preventing leaks, contamination, and equipment failures. Whether sealing temporary pipe openings with rubber pipe plugs or protecting sensitive machinery using rubber hole plugs, these components are vital for operational integrity. This article dives into how modern rubber sealing solutions combine durability with precision engineering.
1. Core Applications of Industrial Rubber Plugs
A. Rubber Pipe Plugs: Guardians of Fluid Systems
Function: bearing seal open ends of pipes during maintenance (e.g., HVAC ducts, oil pipelines)
Pressure Ratings: 20–100 PSI capacity (Viton® plugs for high-pressure hydraulic lines)
Case Example: Food processing plants use FDA-compliant silicone rubber pipe plugs to prevent bacterial growth in CIP (Clean-in-Place) systems
B. Rubber Hole Plugs: Precision Protection
Scenarios:
Covering unused mounting holes in CNC machine frames
Weatherproofing electrical conduits in offshore wind turbines
IP67/68 Compliance: Submersible designs for marine and wastewater treatment plants
C. Customization for Complex Needs
Tailored Dimensions: Plugs from 3mm micro-holes to 200mm large bore pipes
Material Innovations:
Conductive ESD rubber for electronics assembly
High-temperature silicone (up to 230°C) for engine compartments
2. Engineering Advantages of Modern Rubber Plugs
A. Multi-Layer Durability
Structure:
Inner core — High-density EPDM for compression resistance
Outer layer — Textured surface for anti-slip grip
Lifespan: 5–10 years under UV/ozone exposure (third-party tested)
B. Waterproofing Performance Metrics
Zero Leakage: Achieved through radial compression technology
Chemical Resistance:
Chemical Compatibility
Diesel Fuel Excellent
Chlorinated Water Good
Acetic Acid Limited
C. Cost-Benefit Analysis
ROI Data: Plants report 40% lower maintenance costs after switching to modular rubber hole plug systems vs. welded caps.
3. How to Specify the Right Rubber Plug
Step 1: Define Environmental Factors
Temperature:
-50°C to 120°C → Standard EPDM
200°C → Fluorosilicone with metal insert
Media Exposure: Oil-based fluids require NBR; acids demand FKM (Viton®)
Step 2: Dimensional Accuracy
Critical measurements:
Hole/Pipe ID (Inner Diameter)
Depth (For flush vs. protruding installations)
Tolerance: ±0.5mm for press-fit applications
Step 3: Compliance Requirements
Certifications:
NSF/ANSI 61 for potable water systems
ATEX for explosive atmospheres
UL 94 HB flame retardancy
4. Case Study: Automotive Assembly Line Optimization
A Tier-1 auto supplier reduced coolant leakage incidents by 78% using custom-sized rubber pipe plugs with:
Tapered Stem Design: Self-centering insertion for robotic arms
Color Coding: Red plugs for fuel lines, blue for coolant paths
Traceability: Laser-etched QR codes linking to installation specs
Pro Tip: For vibrating environments (e.g., pumps, compressors), combine rubber hole plugs with retaining clips or adhesive primers.
Conclusion
From standard rubber plugs to mission-critical rubber pipe plugs, today’s sealing solutions blend engineering precision with industrial-grade resilience. By leveraging customizable sizes and advanced materials, facilities can achieve leak-free operations while meeting stringent safety standards.
1. Core Applications of Industrial Rubber Plugs
A. Rubber Pipe Plugs: Guardians of Fluid Systems
Function: bearing seal open ends of pipes during maintenance (e.g., HVAC ducts, oil pipelines)
Pressure Ratings: 20–100 PSI capacity (Viton® plugs for high-pressure hydraulic lines)
Case Example: Food processing plants use FDA-compliant silicone rubber pipe plugs to prevent bacterial growth in CIP (Clean-in-Place) systems
B. Rubber Hole Plugs: Precision Protection
Scenarios:
Covering unused mounting holes in CNC machine frames
Weatherproofing electrical conduits in offshore wind turbines
IP67/68 Compliance: Submersible designs for marine and wastewater treatment plants
C. Customization for Complex Needs
Tailored Dimensions: Plugs from 3mm micro-holes to 200mm large bore pipes
Material Innovations:
Conductive ESD rubber for electronics assembly
High-temperature silicone (up to 230°C) for engine compartments
2. Engineering Advantages of Modern Rubber Plugs
A. Multi-Layer Durability
Structure:
Inner core — High-density EPDM for compression resistance
Outer layer — Textured surface for anti-slip grip
Lifespan: 5–10 years under UV/ozone exposure (third-party tested)
B. Waterproofing Performance Metrics
Zero Leakage: Achieved through radial compression technology
Chemical Resistance:
Chemical Compatibility
Diesel Fuel Excellent
Chlorinated Water Good
Acetic Acid Limited
C. Cost-Benefit Analysis
ROI Data: Plants report 40% lower maintenance costs after switching to modular rubber hole plug systems vs. welded caps.
3. How to Specify the Right Rubber Plug
Step 1: Define Environmental Factors
Temperature:
-50°C to 120°C → Standard EPDM
200°C → Fluorosilicone with metal insert
Media Exposure: Oil-based fluids require NBR; acids demand FKM (Viton®)
Step 2: Dimensional Accuracy
Critical measurements:
Hole/Pipe ID (Inner Diameter)
Depth (For flush vs. protruding installations)
Tolerance: ±0.5mm for press-fit applications
Step 3: Compliance Requirements
Certifications:
NSF/ANSI 61 for potable water systems
ATEX for explosive atmospheres
UL 94 HB flame retardancy
4. Case Study: Automotive Assembly Line Optimization
A Tier-1 auto supplier reduced coolant leakage incidents by 78% using custom-sized rubber pipe plugs with:
Tapered Stem Design: Self-centering insertion for robotic arms
Color Coding: Red plugs for fuel lines, blue for coolant paths
Traceability: Laser-etched QR codes linking to installation specs
Pro Tip: For vibrating environments (e.g., pumps, compressors), combine rubber hole plugs with retaining clips or adhesive primers.
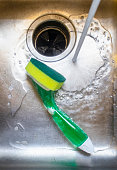
From standard rubber plugs to mission-critical rubber pipe plugs, today’s sealing solutions blend engineering precision with industrial-grade resilience. By leveraging customizable sizes and advanced materials, facilities can achieve leak-free operations while meeting stringent safety standards.
댓글 달기 WYSIWYG 사용