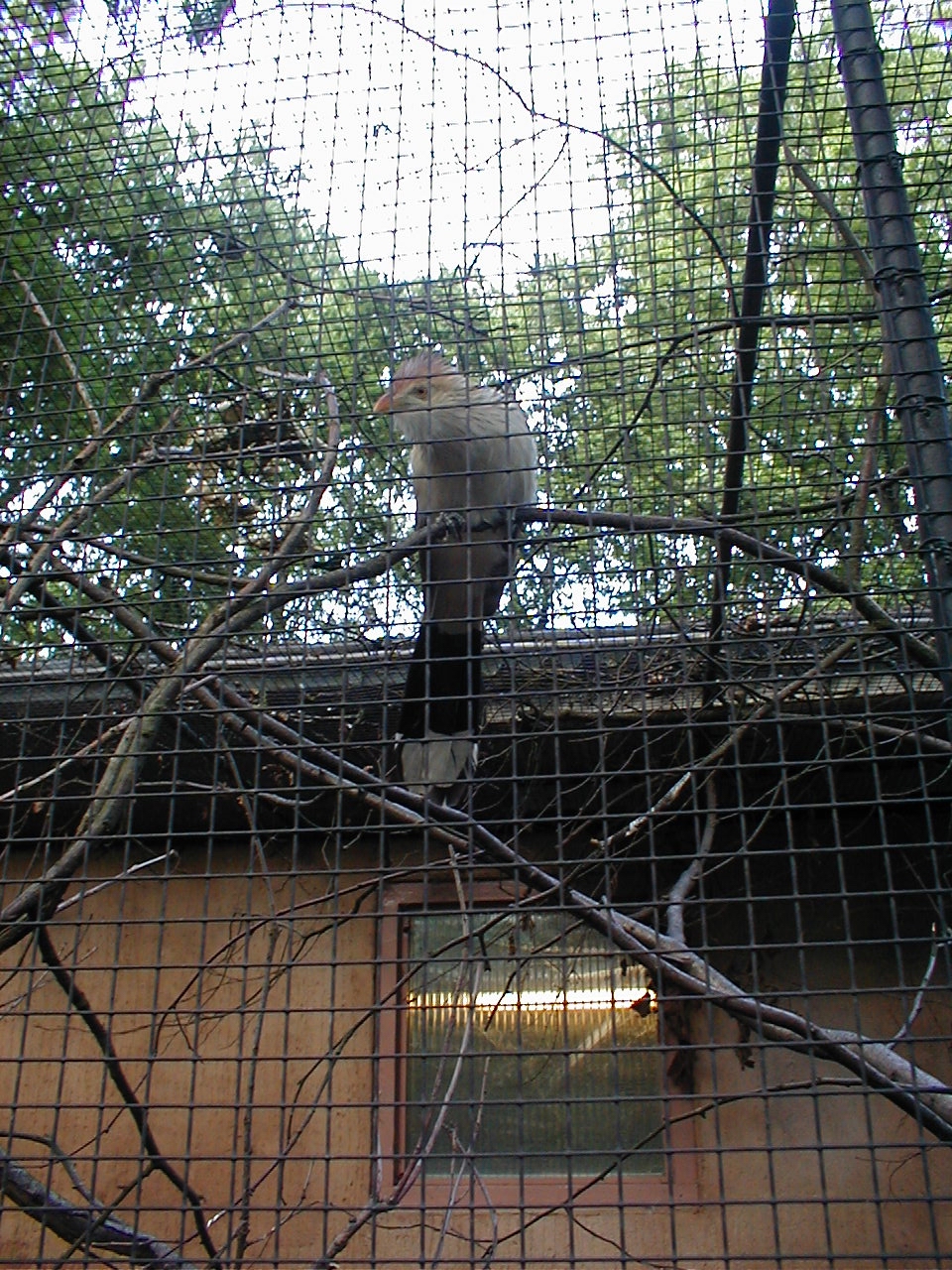
When it comes to designing a filter press for industrial use, scalability is a vital consideration. As production volumes increase, a filter press must be able to handle higher capacities without compromising on quality. This can be achieved through various design modifications, such as optimizing press dimensions.
One key aspect of filter press design that affects scalability is the filter medium's choice. Filter media such as cloth are chosen based on various factors such as fluid viscosity. Selecting the right filter medium and configuring it in an efficient manner can minimize filter press cycles.
The conventional design is also a crucial factor when it comes to scalability. This widely used design uses a series of metal plates bolted to a incline bar frame, over and under which filter cloths are stretched. While this design has been popular, it is not without its drawbacks. Modern designs, incorporating advanced materials plate configurations, offer improved filter performance.
Another important consideration in industrial scalability is the degree of automation of the filter press. Higher automation can provide real-time data, but this also demands more sophisticated control systems. This often comes at a higher upfront cost. However, it can provide enhanced product quality.
To illustrate the impact of filter press design on industrial scalability, consider a facility that needs to expand output by 50% within a short time frame. A poorly designed filter press may struggle to meet this increased demand, resulting in missed production targets.
In final remarks, the impact of filter press design on industrial scalability is multifaceted. Optimizing filter medium configuration, configuring plates and frames effectively, incorporating efficient designs, and implementing high levels of automation can all contribute to achieving efficient scalability. As industries continue to expand, selecting a filter press that meets these scalability demands is critical for long-term success.
댓글 달기 WYSIWYG 사용